About timber in construction
To search all text on this page
On Windows – Press Ctl+F
On Mac – Command+F
Types of structure
- Platform frame construction
- Post and beam
- Hybrid
Wood-based materials and their uses
- Glued laminated timber (glulam)
- Cross-laminated timber (CLT)
- LVL
- Plywood
- Design charring rates
Manufacturing methods
- Panelised construction
- Volumetric timber frame
Types of structure
Timber building structures can be categorised by the stability solution adopted.
Platform frame construction
The term derives from the method of construction that uses floor structures stacked on load-bearing wall panels, creating a ‘platform’ for construction of the next level of wall panels for multi-storey timber structures. Timber frame structures are generally used for low- and medium-rise residential buildings, with CLT used for higher-rise domestic and low-rise non-residential structures.
The external and party walls and room partitions form the vertical and horizontal load paths, making it particularly suited to buildings with regular repeating wall arrangements such as housing, apartments, hotels or student accommodation.
Vertical actions from walls, floors and roofs are supported by timber wall panels of vertical studs at regular centres or by mass timber wall panels. Timber stud walls generally make efficient use of the volume of timber, but will also have a lower load-bearing capacity and robustness compared to solid mass walls, such as CLT or LVL walls.
Resistance to horizontal actions is provided by the in-plane shear (or racking) resistance of sheathed wall panels or mass timber shear walls connected to act as contiguous wall diaphragms.
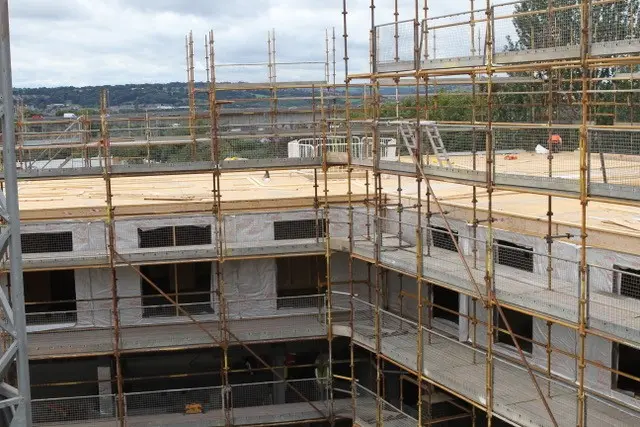
Platform frame construction
Photo: copyright Stewart Milne
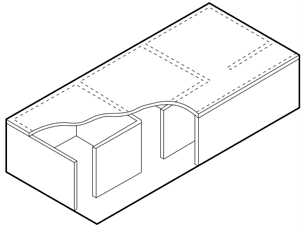
Figure 1: Illustration showing platform frame construction
(Source: TRADA: Structural Timber Elements)
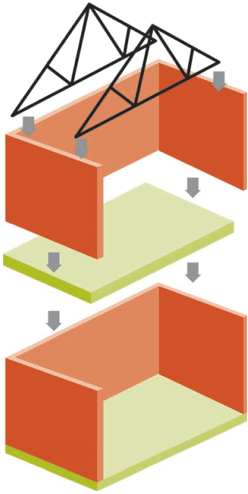
Figure 2: Illustration showing platform frame construction
(Source: STA: Timber Engineering Bulletin 3)
Post and beam
The vertical load from floors and roofs is taken into beams that are supported on columns. Building stability is typically provided by a timber floor acting as a diaphragm to spread the horizontal loads experienced by the building into the vertical stability elements. Such vertical stability elements can consist of timber walls, braced bays or concrete cores. Moment-resisting frames in timber are possible, but rare in construction.
The post and beam method is well-suited to open plan layouts such as offices and recreational buildings, where particular attention should be paid to robustness and disproportionate collapse, as the uses of the buildings often come within critical consequence classes.
The beams and columns are normally formed using engineered wood products, such as glulam or LVL.
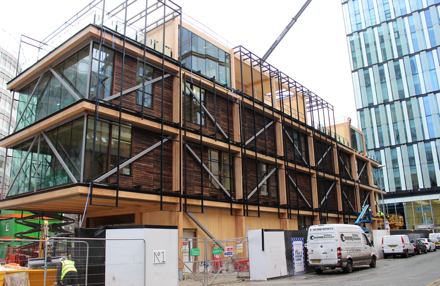
Photo: copyright Stora Enso
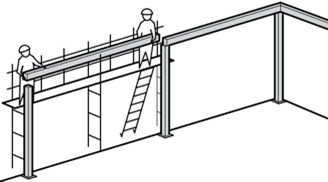
Figure 3: Illustration of typical post and beam construction
(Source: TRADA: Timber Frame Construction 5th Edition)
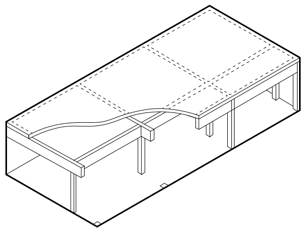
Figure 4: Illustration of typical post and beam construction
(Source: TRADA: Structural Timber Elements)
Hybrid
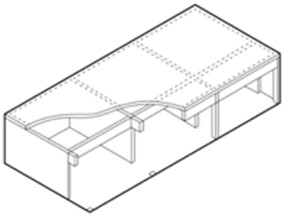
Figure 5: Illustration of typical hybrid construction
(Source: TRADA: Structural Timber Elements)
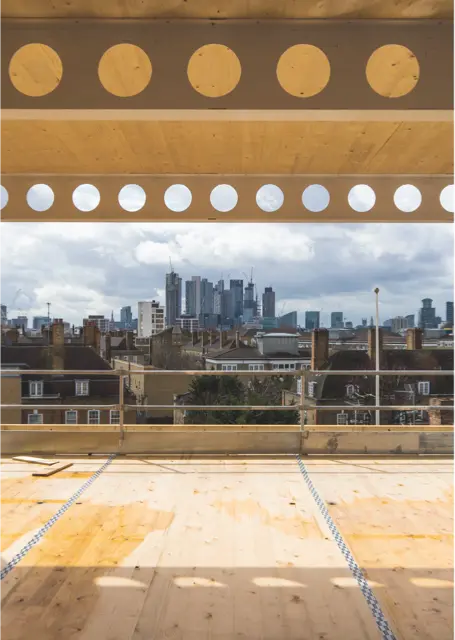
Hybrid steel and CLT.
Photos: copyright Waugh Thistleton architects.
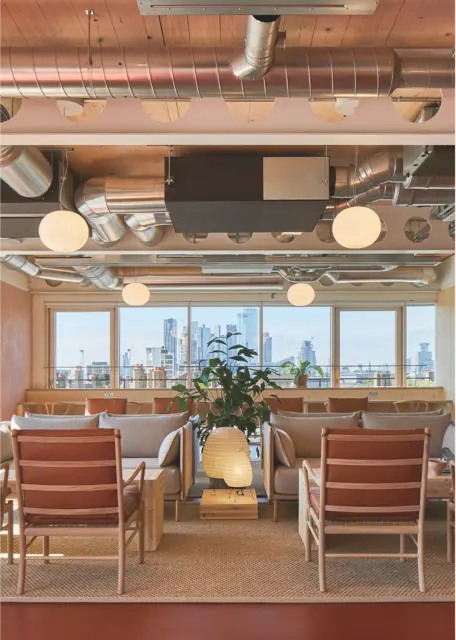
Wood-based materials and their uses
There are many types of wood-based materials used in construction as well as in other sectors like furniture, transport and packaging – from solid wood studs and posts and beams to composite wood products combining materials using nails or other connectors, or where wood shavings or pulp are combined with additives and glues to form new wood-based materials. In some countries wood used in structural products is referred to as timber. In the UK the term timber product or structural timber is most common. Structural timber can be broadly divided into softwood and hardwood. Softwoods come from coniferous (C designation) or evergreen trees, while hardwoods come from deciduous (D designation) or broadleaf trees.
Traditionally, the size of structural timber members was limited by the size of the parent tree. Typically, the largest sawn timber elements currently available have a cross-sectional dimension up to 0.30 m and a length up to 6.0 m. During the processing of trees into timber, strength-reducing features (most commonly knots and slope of grain) are identified that determine the type of timber product they are suitable for.
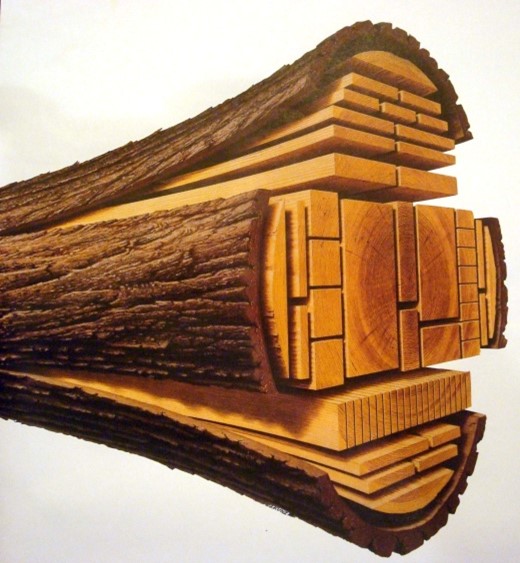
Figure 6: The division of round wood into structural timber elements
Longer lengths can be produced by finger-jointing.
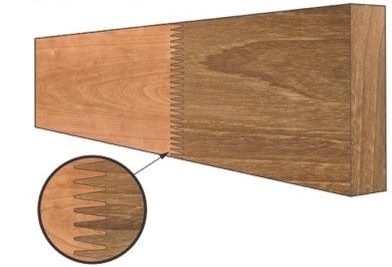
Figure 7: Finger-jointed sawn timber elements
(Source: STA: Timber Engineering Bulletin 3)
However, with modern structural adhesives and manufacturing processes, the size of structural timber elements is limited by what can be easily manufactured and transported; cross-laminated timber (CLT) panels are now available up to 500 mm thick by 3.5 m wide by 16.5 m long.
Processed timber elements are known collectively as ‘engineered wood products’ (EWPs) – a family of products rather than one specific material, see Figure 8.
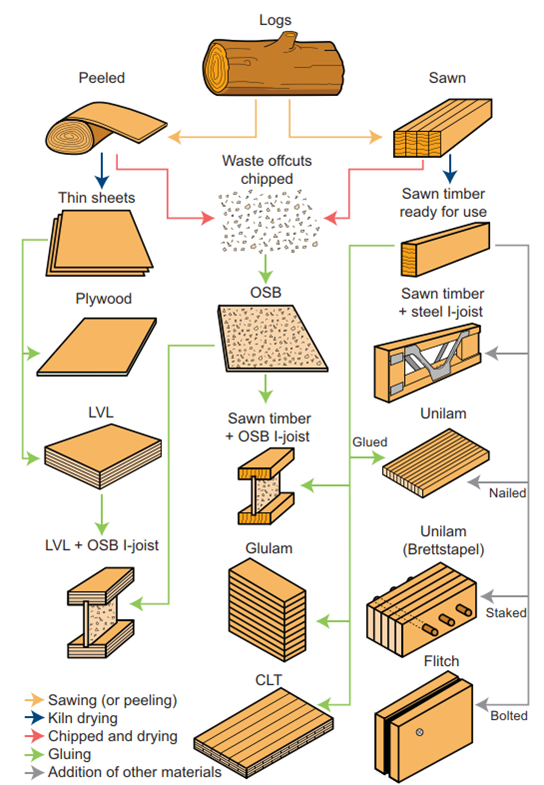
Figure 8: Family of timber products
(Source: TRADA Structural Timber Elements)
During the processing of trees into timber, strength-reducing features (most commonly knots and slope of grain) are identified that determine the type of timber products they are suitable for. To determine the strength of timber, and its potential uses, the timber is graded into different groups with similar structural properties, often referred to as ‘strength-grading’. This can be done visually or using machines using rules described in a number of standards (EN14081, BS5756 and BS4987). Strength grades for softwood range from C14 to C50 and hardwood from D18 to D70. Timber used in trussed rafters is designated in TR classes (most commonly TR26).
In the UK the most commonly used species are pine, spruce and larch in strength classes C16 and C24.
Click here for more information on strength-grading.
Structural timber will generally be from trees that have been managed throughout the growing period to minimise knots and slope of grain. Engineered wood products can utilise trees, or the parts of trees, that have more of these imperfections, by cutting them out and re-jointing or laminating lower grades of timber together to make stronger, more homogeneous elements. Innovation in manufacturing and gluing technologies optimise the use of all material generated by trees.
Engineered wood products are differentiated by their manufacturing process, the load-bearing capacity of the products, and their applications. Heavy load-bearing applications will require timber products like Glulam or LVL, whereas roofs and floor joists in domestic applications will often use I-beams or open-web joists. An overview of the main features of each commonly-used product in the UK (and elsewhere) is shown below.
Glued laminated timber (glulam)
A structural member made by gluing together a number of graded timber laminations with their grain parallel to the longitudinal axis of the section. Members can be straight or curved, horizontally or vertically laminated, and can be used to create a variety of structural forms (columns, large-span beams, floors and roofs).
Laminations are typically 25 mm or 45 mm thick. Most commonly, glulam is made from 40 mm thick layers. In tightly curved or vertically laminated sections smaller laminations can be used. The requirements for glulam manufacture are contained in product standard BS EN 14080.
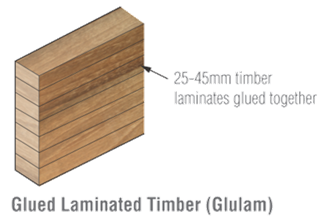
Figure 9: Illustration of Glued Laminated Timber (Glulam)
(Source: STA Timber Engineering Bulletin 2)
Cross-laminated timber (CLT)
A product used in high load-bearing applications with a minimum of three cross-bonded layers of timber, each layer having a thickness between 6 mm and 45 mm. Laminations or lamellas are strength-graded to BS EN 14081-1 and glued together in a press that applies pressure over the entire surface area of the panel.
CLT panels typically have an odd number of layers (3,5,7,9), which may be of differing thicknesses but are arranged symmetrically around the middle layer with adjacent layers having their grain direction at right angles to one another.
Adhesives
Fire design of glued timber elements has to consider the type of adhesive used. This is especially true for cross-laminated timber (CLT), which may show falling off of charring layers (“delamination”) at fire exposure. Heat-resistant adhesives (i.e. without delamination) are mainly phenolic and amino-plastic adhesives, but some polyurethane adhesives are also now available. The fire performance of a specific adhesive depends on the chemical composition rather than the group of adhesives it belongs to. Since not all producers of CLT use heat-resistant adhesives, it is important to verify that the material is produced with heat-resistant adhesive if required.
The requirements for CLT manufacture are contained in product standard BS EN 16351 (not yet harmonised).
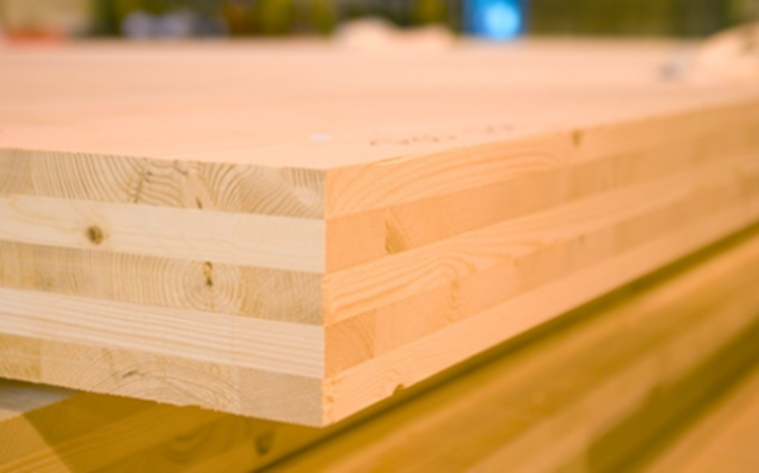
Figure 10: Illustration of Cross-laminated timber (CLT)
(Source: STA Timber Engineering Bulletin 2)
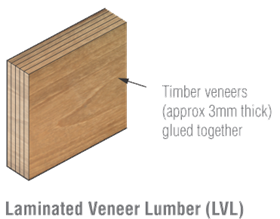
Figure 11: Illustration of laminated veneer lumber (LVL)
(Source: STA Timber Engineering Bulletin 2)
Particleboards and fibre composites
An EWP manufactured with flanges made from softwood or LVL with glued thin webs, generally made from OSB, fibreboard or plywood.
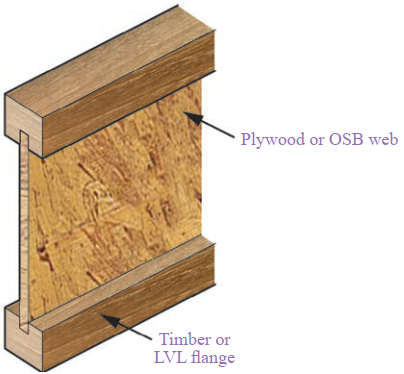
Figure 12: Illustration of I-joists
(Source: STA Timber Engineering Bulletin 2)
These are shallow parallel-chord trusses manufactured with flanges (or chords), usually made from softwood, with metal or timber strutting to form the webs (see figure 13).
The chords (and webs where timber webs are used) are generally planed softwood graded in accordance with BS EN 14081-1. The strength class of the timber is usually C27 in accordance with BS EN 338:2009 or TR26. The depth of the chords is generally 47 mm and their widths range from 72 mm to 145 mm. Metal webs are typically profiled, using nominal 1mm galvanised light gauge steel with a zinc coating specification of Z275.
Open web joists are principally used as a roof or floor joist element. They are preferred to I-joists in highly serviced buildings since they offer a combined services and structural zone.
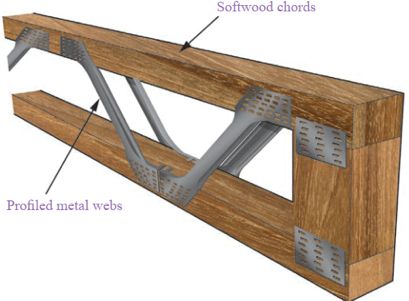
Figure 13: Illustration of open web joist
(Source: STA Timber Engineering Bulletin 2)
Manufacturing methods
Wood construction in Europe and the UK has a long and enduring history. The oldest timber building in the UK, still in use today, has been dated (by dendrochronology) as having been built between 1277 and 1297. Timber construction techniques have adapted and changed over the years, with many innovations and technological advances.
The construction technique of ‘timber frame’ has been popular for centuries. The modern type was introduced to the UK from Sweden in the 1920s. In the late 1930s the first trials of timber frame were in Scotland where the timber could be readily sourced and construction could be progressed quickly in potentially adverse weather conditions. It is believed that by 1940 over 3,000 homes had been built in timber frame throughout the UK. World War II delayed the further spread of timber frame. In 1963 the Canadian timber frame house practices were introduced to the UK and up to 1973 these were adapted and calibrated to UK practice and environment.
Throughout the 1990s organisations such as BRE were active developing best practice guides to support the timber frame industry. This was further supported by the TF2000 project, which started in 1996, where timber frame type construction was to show its suitability for medium-rise construction and pave the way for the industry to build on the achievements of the past decade and further expand into new, previously untapped markets.
Building practices in timber are flexible mainly due to the variety of timber building elements, from timber studs in varying sizes and strengths to joists and glued elements. A large range is available from a variety of sources, from building merchants to specialist suppliers. The construction process can take many forms, from elemental construction, where single timber and other materials are assembled on site, to complete off-site manufactured solutions and varying degrees of finishing in between. Some of the most common techniques are summarised below.
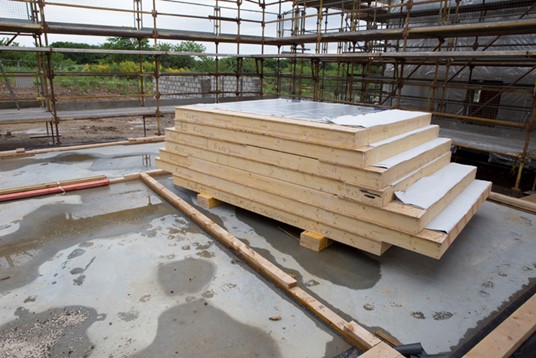
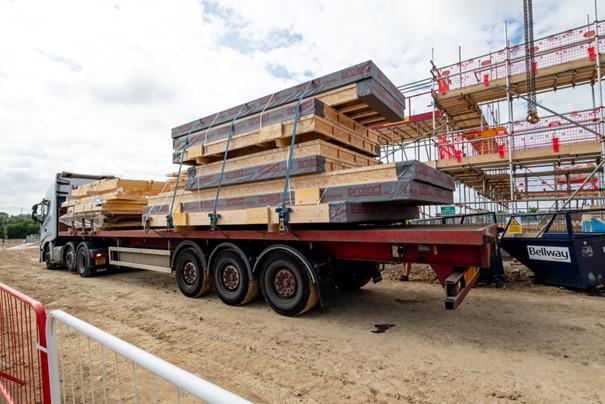
Panelised construction
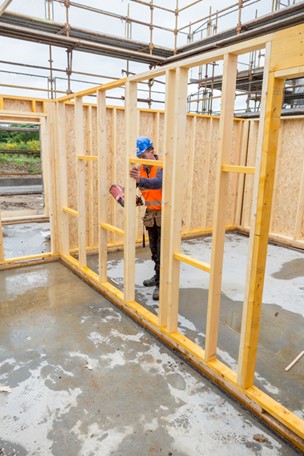
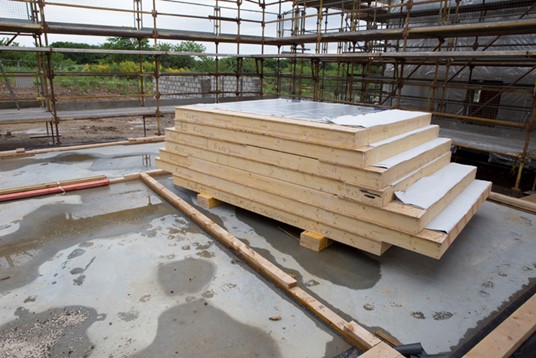
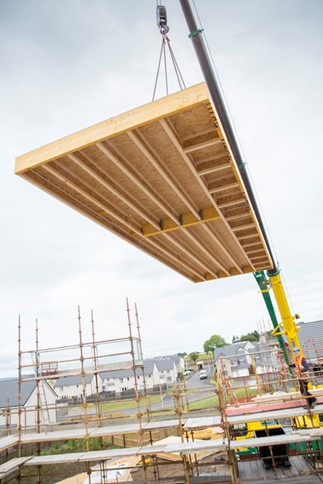
Open panel
Timber frame wall panels of studs and rails, with sheathing on one face and a breather membrane.
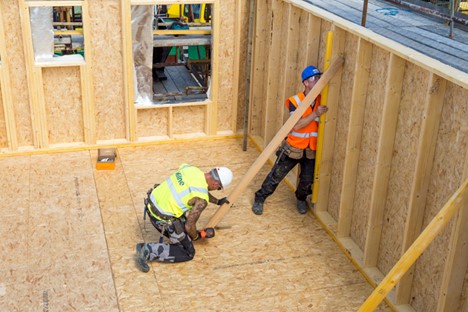
Pre-insulated panel
As open panels but with insulation between the wall studs.
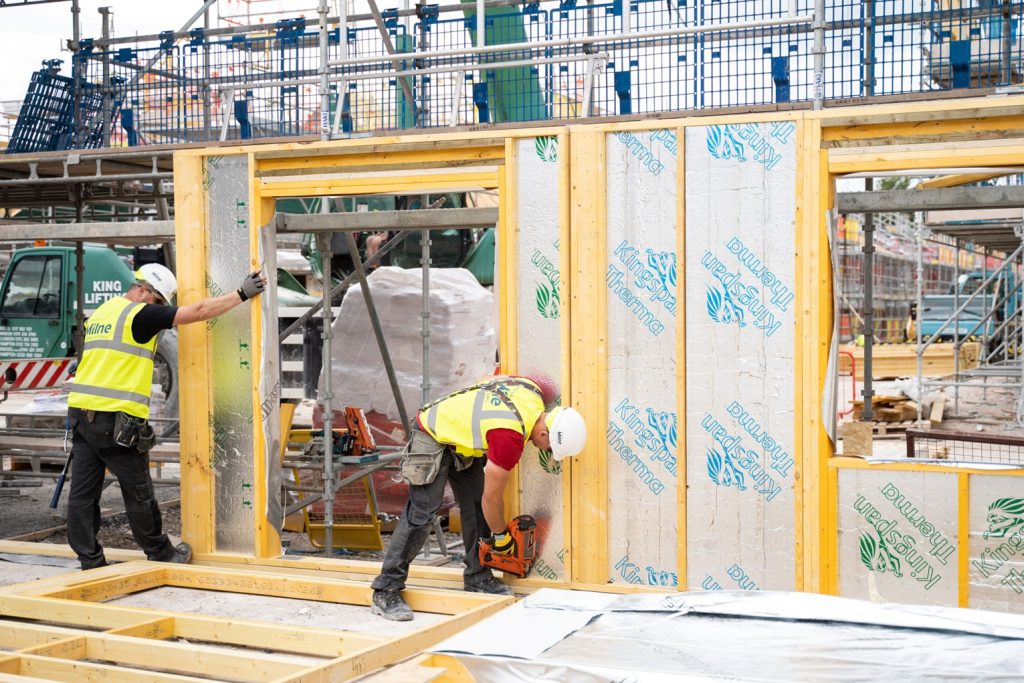
Closed panel
Timber frame wall panels of studs, rails and insulation with sheathings and/or linings on the faces of the panel. There is a vapour barrier on the warm side of the insulation and a breather membrane on the outer face of the panel. Closed panels may also include fitted windows and internal service zone battens.
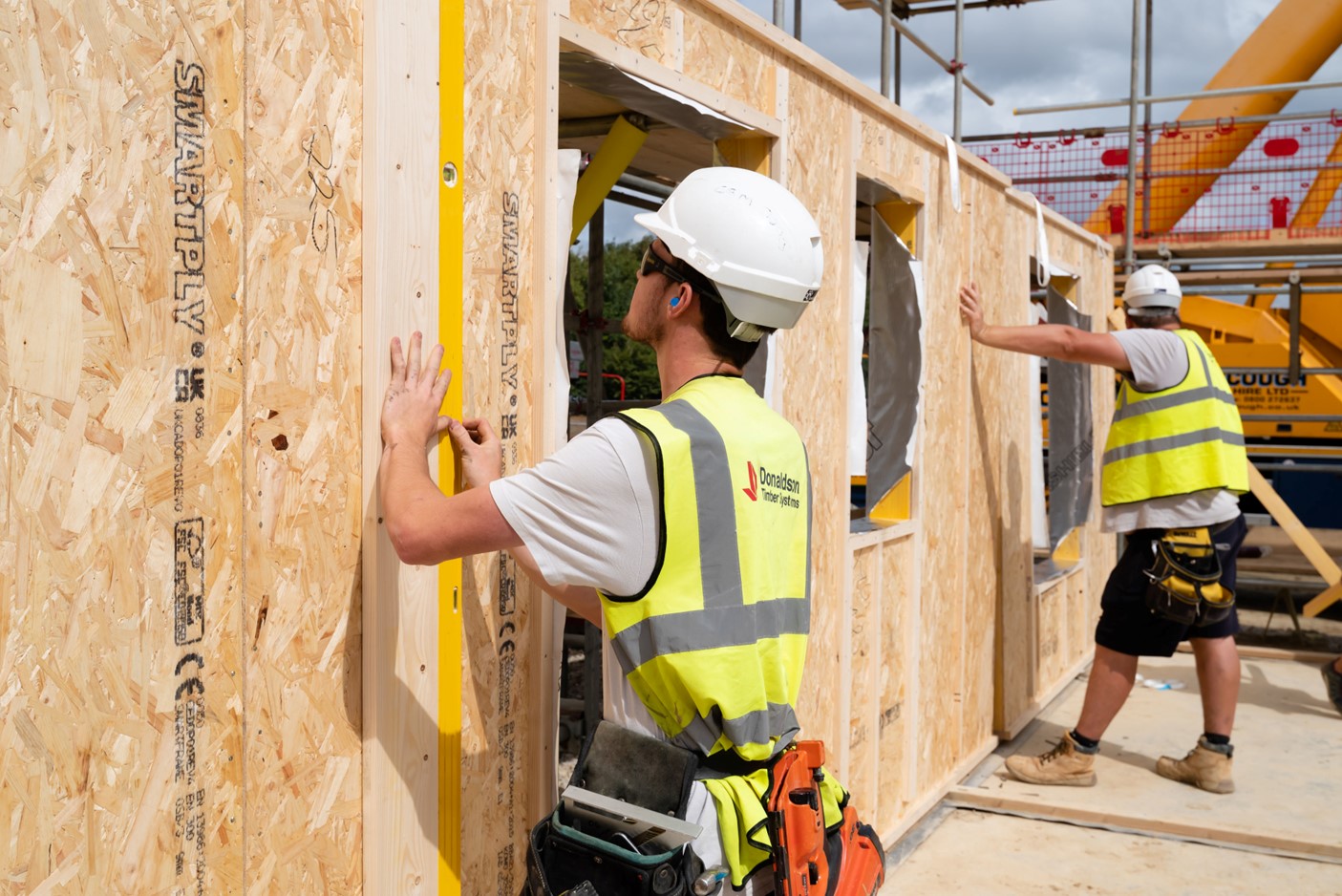
SIPs
Structural insulated panels (SIPs) are composite members that use a core of rigid insulation between plywood or OSB face layers, not only to provide insulation for a building’s thermal envelope, but also to form a composite structural panel to resist in-plane and out-of-plane forces.
Cross-laminated timber (CLT)
The characteristic feature of structural components in CLT – for walls and floors – is their size. Large cross-sectional areas ensure that CLT components have a high load-bearing capacity and stiffness, making them suitable for stabilising the building. The panels are available with a high degree of prefabrication, and their low weight brings benefits in terms of groundwork, transport and assembly.
Making openings and attaching fixings is simple and straightforward. The low weight of CLT panels makes them significantly easier to handle than concrete panels. Fixings and foundations are also made easier, which is of benefit when redeveloping existing buildings.
Volumetric timber frame
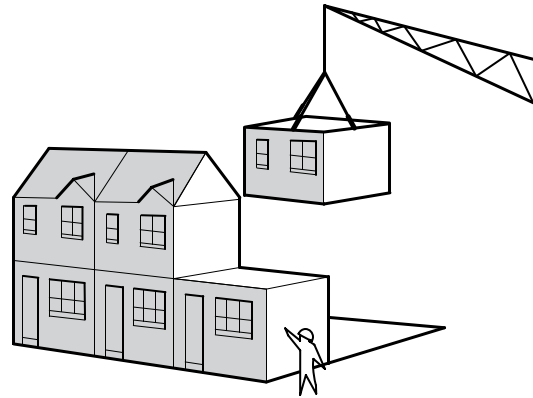
Figure 14: Illustration showing volumetric construction
(Source: TRADA: Timber Frame Construction 5th Edition)